How General Drilling, Inc. Raised Safety Standards and Cut Delays with Device Magic
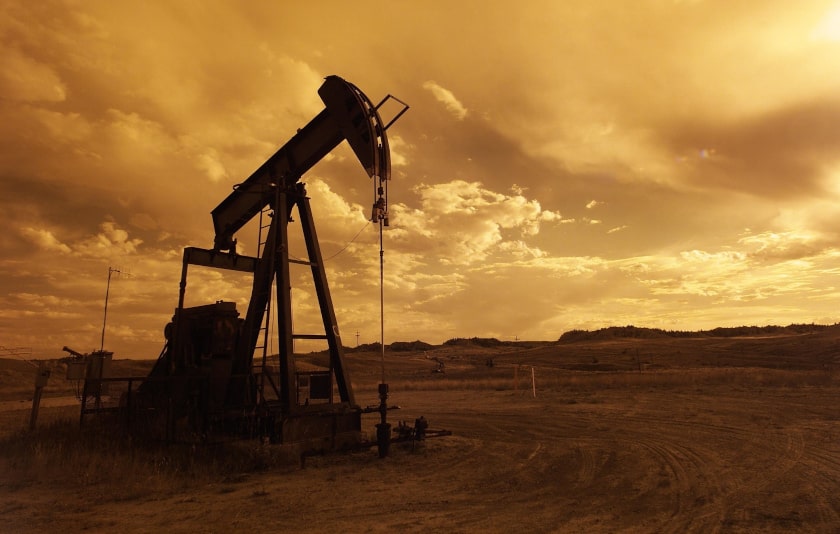
For more than 45 years, General Drilling, Inc. has provided safe, reliable, expert solutions to the blast-hole drilling needs of stone quarries. Their fleet of over 29 track and truck-mounted drill rigs service quarries throughout Indiana, Kentucky, western Ohio, eastern Illinois and northern Tennessee. GDI prides themselves on well-maintained rigs, experienced staff, a commitment to performing the best job possible and above all, the safety of their personnel and customers.
The Challenge: Maintaining Compliance
Gus Diehr, Treasurer and CFO of General Drilling, says the company turned to Device Magic to stay compliant, specifically in relation to date, time and safety regulations. Prioritizing employee safety is number one for GDI, which regularly enrolls their staff in training opportunities like hearing protection programs and provides no shortage of quality, personal protective equipment.
This is key considering the fact that, according to the National Safety Council, a worker is injured on the job every seven seconds, adding up to 510 injuries per hour, 12,600 daily, 88,500 each week and 4.6 million every year. In the U.S. in 2017 alone, 104 million production days were lost due to work-related injuries. Coupled with this, the indirect costs of workplace incidents, such as time lost due to work stoppage and investigations, are estimated to be 2.7 times that of direct costs.
As a result, General Drilling uses mobile inspection forms and safety checklists to uphold their safety and quality standards, and to keep these numbers low. “We routinely audit all employees in the field to ensure that they meet regulations and our customers’ expectations. Our drills are bore tracked at least twice a year to make sure the equipment level is working properly,” Diehr explains. “We routinely audit all employees in the field to ensure that they meet regulations and our customer’s expectations.”
He adds that another big pain point for General Drilling was the time it took to deliver and process paperwork that teams completed in the field. Delays in receiving any of the many data points in the drilling and mining industry often result in regulatory, safety or billing issues. These are precisely the problems General Drilling actively works to avoid.
“We run remote operations, and in the past, getting info from our employees back to the office was cumbersome,” Diehr says. “There was sometimes a 1-2 week delay.”
The ability to speed up data delivery and access with Device Magic, as well as the capacity to capture proof of work onsite through photos and signatures, were additional key benefits. Furthermore, a recent study found that utilizing mobile inspection forms led to a 23% reduction in incidents.
“We’ve got daily job updates, condition of equipment reports, daily driver logs and general inspections. Device Magic gets what we need as an organization that runs remote operations,” Diehr explains.
“We need to have everything submitted electronically in real-time. We need to be able to collect data without an internet connection. Device Magic is doing everything we need it to do.”
Increasing Efficiency, Quality Assurance and Safety Levels
To understand how Device Magic would work within their environment, the General Drilling team began by signing up for a free trial and testing the software in the field. Soon afterwards, the company rolled out Device Magic mobile forms to over 40 employees. And before long, they saw the cumbersome delays and resulting compliance issues fade away.
Instead of waiting on a safety checklist from a quarry to arrive at the office, real-time data capture ensured that information was delivered as soon as a field employee submitted it. After a form was completed following an inspection, a PDF containing all the data was instantly generated and emailed to the appropriate recipients. Waiting days to receive the information was reduced to seconds. General Drilling’s improved log submissions process is a great example of this heightened efficiency. As detailed on their website, “We provide our customers a drill log for every shot after it is drilled. This drill log can be electronically sent to as many people as needed, and explosives personnel can have the drill log before they show up on the site. Our whole goal is to get your work done as safely and as fast as possible.”
With Device Magic, the company has successfully eliminated the need to manually file and manage paper invoices, daily job updates, inspections and safety reports. “We need to keep all of that information on record. Now, not only is it delivered to the people who need it, but it’s also automatically stored in our cloud-based storage service for archival purposes,” Diehr says.”Waiting days to receive the information was reduced to seconds.”
Organizations with remote teams and threatening working conditions like General Drilling understand just how critical real-time data capture is. Not only does it ensure that accurate information is delivered immediately, but it also empowers these businesses to optimize their safety systems and minimize the occurrence of harmful incidents.
In doing so, they are able to operate at a much higher efficiency rate and ensure quality assurance, as well as keep their personnel safe and their customers satisfied. With the help of Device Magic, General Drilling has been able to do just that.