How To Create A Better Preventive Maintenance Checklist
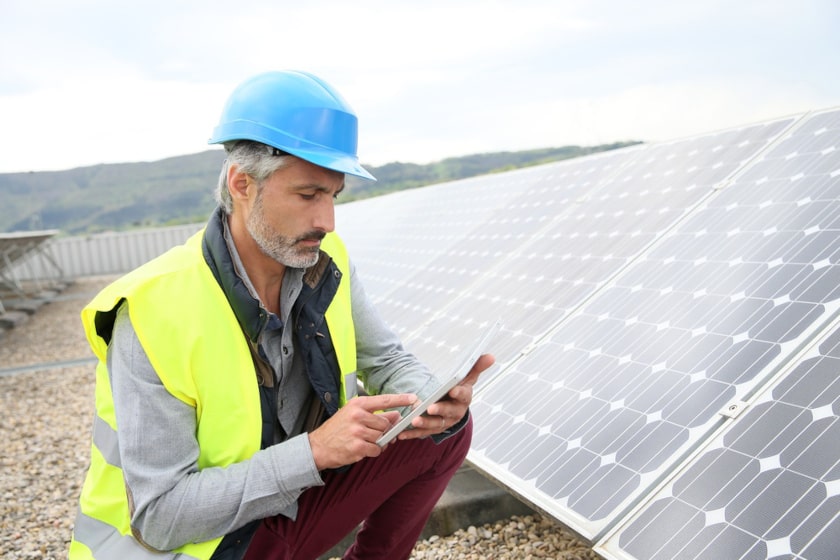
A checklist is a proven way to increase quality and make sure that work is completed thoroughly. But what exactly is worth including on your preventive maintenance checklist?
We’ll guide you through the process of writing a simple, money-saving checklist for your staff.
Why Do Preventive Maintenance Checklists Matter?
You might appreciate the value of preventive maintenance after a major equipment failure or system breakdown occurs at your property or site. But what if you need to convince your managers to fund your preventive maintenance program?
To help you make the pitch, consider the following case study from Texas Instruments. Texas Instruments set a goal of “zero major interruptions” in 2008. From a mechanical perspective, the Dallas campus completed the year achieving goal of zero.
The cost difference, when comparing interruptions for 2007 vs. 2008, exceeded $12 million. That’s a major cost savings by avoiding errors and interruptions.
Phase 1: Assess Your Environment
To create an effective preventive maintenance checklist, you need to understand your environment. Use the “SWOT” (Strengths, Weaknesses, Opportunities, and Threats) framework to quickly assess where you are starting from.
Scenario: Your company is responsibile for maintaining telecom infrastructure. In your role as the maintenance manager, you are looking for ways to improve your team’s effectiveness.
- Strengths: Your staff are well trained and motivated to carry out their work.
- Weaknesses: Reliance on paper forms and out-of-date forms causes you to receive responses of questionable value.
- Opportunities: Next month, your maintenance portfolio will include five new facilities because your company won new business. Sustaining quality during this expansion will be a key test of your leadership.
- Threats: Some of your end clients complain about paying for expenses when there is nothing wrong. Demonstrating the value of your preventive maintenance program is one solution you have considered.
Now that you are equipped with this information, you will be able to create a checklist tailored to your work.
Phase 2: Create a Draft Checklist
The art of successful maintenance requires making choices. If you assign your staff to carry out an in-depth inspection of site A, they will be unavailable to inspect other sites. Keep that in mind if you feel anxious that your efforts may not cover every asset in your building.
Continuing with the telecom maintenance example above, here are some of the ideas you can put into your checklist:
- What are the high value assets? For telecom, you may choose to focus on infrastructure and equipment exposed to the elements.
- What are the leading indicators of asset failure? Combing through user reports, you may find that connectivity becomes intermittent for several weeks prior to complete failure. Detecting that type of connectivity failure is a good way to be proactive about problems.
- What are “quick wins” for preventive maintenance? Ask your field staff for suggestions in this area. If your staff are involved in creating a checklist, they are more likely to use it.
- What important checks are neglected when staff are under pressure? This will be a key question for you as your company expands to care for additional facilities or sites.
Phase 3: Test the Checklist
At this stage, your preventive maintenance checklist may have a half dozen items and questions in place. You’ve already focused on high value assets, taken staff comments into account and looked at leading indicators.
Now it is time to test your checklist with the following steps:
- Read the checklist backwards to double check for issues. This proofreading technique helps identify errors.
- Test the checklist yourself. The best approach is to use the checklist in an unfamiliar environment where you will focus on each step.
- Ask two other people to use the checklist and provide feedback.
- Prepare adjustments to the checklist as required based on the feedback you receive.
Phase 4: Introduce the Checklist
If the preventive maintenance checklist is a new process for your team, you will need to guide your staff through it and train them to use to effectively.
Use the following tips to introduce your team to the document. If your staff are based at the same location, organize a short staff meeting to explain the process.
- Start with why. Explain that prevention is an excellent way to minimize accidents and save money by avoiding more costly repairs.
- Summarize how you developed the checklist. Your staff will feel more confident about using the checklist once they hear that it has already been tested in the field.
- Answer questions and provide support. Encourage your employees to ask questions now so that they avoid becoming confused in the field.
- Issue the checklist to your team. Using a digital form system for data collection is a great way to both introduce the checklist and keep it easily accessible for your team.
Keep your checklist at your fingertips with mobile forms. It’s easy to get started. Sign up for free.