Top 10 OSHA Violations & How to Avoid Them in 2020
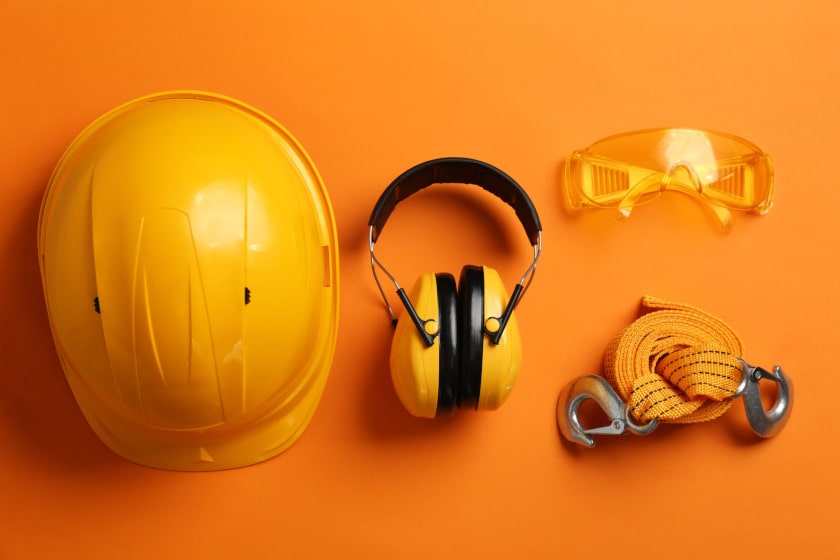
Providing a safe work environment for employees should be a priority for your company. When compliance is overlooked and workers aren’t trained properly or act carelessly, an accident or injuries can easily occur. Compliance with safety regulations will help your company to avoid accidents and costly OSHA violations that will stall your project or worse, shut down a work site. In this post, we’ll cover the top 10 OSHA violations and how to avoid them in 2020.
“The OSHA Top 10 is more than just a list. It is a blueprint for keeping workers safe. When we all work together to address hazards, we can do the best job possible to ensure employees go home safely each day.” – Deborah A.P. Hersman, President and CEO of the National Safety Council
Top OSHA Violations
Here’s a quick list at the top OSHA violations. We’ll provide a closer look at each below along with some tips on how to avoid them:
- Fall Protection – General Requirements
- Hazard Communication
- Scaffolding
- Lockout/Tagout
- Respiratory Protection
- Ladders
- Powered Industrial Trucks
- Fall Protection – Training Requirements
- Machine Guarding
- Eye & Face Protection
- Electrical – Wiring Methods
This list is a great place to start to evaluate safety on your own jobsite or workplace. Doing so will help you to avoid potential OSHA violations and expensive fines. This will also help you to be prepared if an OSHA inspector shows up at your site.
Device Magic can help you complete site inspections, audits, and compliance reports faster with mobile forms. Learn more
OSHA Violation Breakdown
Let’s take a closer look at each of the most common OSHA violations noted above:
Fall Protection – General Requirements
Every year, over 300,000 people are injured due to a fall in the workplace. This happens most commonly on construction sites, but the risk of slipping and falling is something every business needs to take very seriously. To avoid this extremely dangerous workplace risk:
- Keep walking surfaces clean and free of clutter
- Lighting and signage
- Require proper footwear
- Regularly inspect scaffolding and other susceptible areas
Hazard Communication
OSHA requires companies to have a hazard communication plan in place to keep everyone safe and accountable. An OSHA compliant Hazards Communication plan consists of four parts: a written program, appropriate labels and warnings, datasheets for material safety, and comprehensive hazard communication training. This allows employees to be clear about the hazards of the chemicals they are exposed to when working.
To avoid an OSHA violation:
- Educate employees on Hazard Communication labels around the workplace and what they mean
- Educate employees on how to detect the presence or release of a hazardous chemical in the work area and what to do if they find themselves in this situation
- Educate employees on the procedures you have in place to protect them from exposure to hazardous chemicals. This includes safe work practices, how to handle a hazardous materials emergency, and how to use/access personal protective equipment.
Scaffolding
Scaffolds are a necessary type of equipment used on most construction sites to help workers build, repair, and clean specific structures. They are essential to help workers reach projects that are high off the ground, but they can put workers at risk of slipping, falling, or being struck by falling objects.
OSHA has established specific standards to regulate the design, use, and construction of on-site scaffolds. To avoid this type of OSHA violation:
- Ensure all scaffolds higher than 10 feet have guardrails
- Use step stools and ladders to ensure workers can safely get off and on to the scaffold
- Check for gaps between the planking and decking that could cause a fall
- Check that the foundation of the scaffold is placed on something solid such as level gravel or crushed rock.
Device Magic makes it easy to keep track of your inspections. Use our free inspection report templates, or create custom forms to meet your unique requirements. Learn more
Lockout / Tagout
Lockout / Tagout (LOTO) procedures are in place to ensure that hazardous energy is not expelled during the service or maintenance of equipment and machinery. It also helps to prevent the unexpected energization or startup of machinery and equipment. According to OSHA, a Lockout / Tagout involves “authorized employee(s) either locking or tagging the energy-isolating device(s) to prevent the release of hazardous energy and take steps to verify that the energy has been isolated effectively.”
One of the easiest ways to prevent injury on the job is to ensure that all machinery and equipment is disabled when not in use, so it doesn’t start up accidentally. To avoid this type of OSHA violation:
- Get all of your employees on the same page. Many times, a lockout / tagout violation is not due to an employer’s negligence, but instead due to employees not being trained on the risks and procedures associated with LOTO. Require all employees to go through a LOTO training program.
- Perform regular inspections to audit all machinery and equipment, especially when there is a new piece of equipment in the workplace. Identify all sources of energy, not just electricity. A pulley could technically be a source of energy and could result in an accident if not stored and handled correctly.
- Don’t buy cheap equipment. Investing in durable and reliable machinery and equipment is much more cost-effective than paying thousands of dollars in OSHA violation fines—or workers compensation claims.
Powered Industrial Trucks
Incidents involving powered industrial trucks or forklifts consistently rank among the top 10 OSHA violations. OSHA requires any company using a forklift to have procedures in place regarding “hazard identification and solutions, supervision, operating procedures, maintenance and repair procedures, facility design, and forklift selection criteria.”
The improper use of a forklift could result in serious damages, injury, and even death. To avoid this type of violation:
- Develop a training program that identifies the type of workplace forklifts and which employees are authorized to use them.
- Set clear rules and restrictions on how and where a forklift can be used.
- Ensure adequate licensing. Ensure everyone who operates this equipment meets all the designated requirements and has the appropriate licensing.
Fall Protection – Training Requirements
Your company can be found in violation of OSHA standards if you don’t have a fall protection training program in place. Falling off of scaffolding or a tall ladder is not the only fall risk in a workplace. Many workers are injured when falling into an excavation site or in other situations as well.
To avoid this violation:
- Understand the four different levels of fall protection training requirements: awareness, authorized-user, competent person, and qualified-person training
- Ensure that all employees go through authorized-user training to comply with OSHA standards and regulations
- Keep good records. Detailed training records, such as dates and employee attendance, are required in some OSHA mandates.
Machine Guarding
Machines that are not guarded correctly put workers in harm’s way. Employees could be injured by flying pieces, sparks, and moving parts when machines do not have a safety guard in place. Some examples of machines that require the use of safety guards include transmission shops, flywheels, belt tighteners, portable saws, and more.
To keep employees safe and avoid this type of violation:
- Use safety guards. Make sure every machine that needs a safety guard has a safety.
- Watch pinch points. Keep guards away from pinch points.
- Train your workers. Provide adequate machine guard training so your workers know how to use these devices properly.
- Stay on top of preventive maintenance. Keep your machine guards maintained, and ensure all employees understand the importance of replacing machine guards after their removal for maintenance.
Eye & Face Protection
When a job requires an employee to come in contact with chemical, environmental, or radiological hazards, eye and face protection must be provided. Workers must go through a workplace hazard assessment and undergo training to ensure their health and safety. The training should include details on when this equipment is necessary, what equipment to use when, and the proper care, maintenance and disposal of the equipment.
Neglecting to train employees about the appropriate use of eye and face protection could result in severe injuries, blindness, and even death. To avoid this common type of OSHA violation:
- Make sure there are emergency eyewash stations in all areas that are considered hazardous.
- Post first aid instructions and procedures in areas of the workplace that could potentially be dangerous.
- Conduct workplace training that covers the proper care and use of personal protection equipment.
Electrical – Wiring Methods
Electrical equipment and wiring systems that are improperly installed can create a dangerous workplace environment. Faulty wiring methods can lead to blown circuits, fires, and electrocution. OSHA lists the following as the most frequent causes of electrical injuries: “contact with power lines, lack of ground-fault protection, the path to ground missing or discontinuous, equipment not used in the manner prescribed, and improper use of extension and flexible cords.”
To avoid this type of violation:
- Train employees on how to spot potential hazards and familiarize employees with the proper use of extension cords.
- Provide guidelines for appropriate maintenance and storage of power tools.
- Regularly inspect heavy machinery to make sure there is no risk of it coming in contact with live wires.
- Provide ladders that are not made of metal for employees who work with power lines.
More Tips to Avoid OSHA Violations
Here are a few more general tips to help you avoid top OSHA violations:
Document Procedures
Make sure that everyone at your company is aware of OSHA standards and guidelines so they can better follow them. One of the most important things you can do to avoid potential OSHA violations is to create a plan to deal with these hazards, and to train your employees sufficiently. Keep safety plans and procedures well documented and accessible to employees.
OSHA also provides training materials and resources to help you stay compliant and to create procedures for your company.
Identify Hazards
Violations related to falls and fall hazards consistently top OSHA’s list. Workers need to be able to safely access all areas on a jobsite or in the workplace to complete tasks. Guardrails, safety harnesses, railings, secure scaffolding and not having open areas are all steps you should take to protect workers.
In order to minimize risks for everyone on your site, it’s important to complete a job safety analysis. Each job safety analysis should outline the hazards of the job being performed, as well as what steps will be taken to prevent injury to the people completing the task. Once documented, this information can be used in employee training and can help you to be OSHA compliant.
Provide Sufficient and Frequent Training
Make sure that everyone at your company is aware of OSHA standards so they can better follow them. This is one of the most crucial areas to focus on to avoid violations. A lack of employee training is more likely to lead to an accident.
Provide training for all employees on using equipment and general safety procedures. Also, make sure that your documentation and training materials are updated regularly.
Safety training shouldn’t be limited to employee on-boarding. It needs to be consistently discussed and emphasized. Hold safety trainings every few months to keep the information fresh in employees’ minds. Creating a culture of compliance and safety will help your company to avoid dangerous situations and costly delays.
Consider Using Mobile Forms
Complete site inspections, audits and compliance reports faster with mobile forms. Learn more